What Are Logistics and Distribution Safety Audits?
Safety audits in logistics and distribution involve a thorough review of the systems, procedures, and practices that govern how goods are handled from the moment they leave the supplier until they reach the customer. These audits look at everything from the physical security of storage facilities to the accuracy of inventory management and the effectiveness of staff training. The goal is to identify risks—such as potential theft, equipment malfunction, or procedural errors—and recommend steps to address them. With the increasing complexity of supply chains, these audits have become a vital tool in maintaining operational integrity.
Why Do Safety Audits Matter for Logistics and Distribution?
In a sector where even minor issues can disrupt the flow of goods and lead to substantial financial losses, safety audits play a crucial role. When audits are conducted regularly, they help catch problems early. For instance, if a particular warehouse consistently shows discrepancies in inventory, an audit can pinpoint whether the issue is due to administrative errors or something more serious like theft. By addressing these issues promptly, companies can reduce downtime and avoid costly disruptions. The insights gained from these audits provide a clear picture of where improvements are needed, ensuring that every link in the distribution chain is secure and functioning as intended.
How Can Organizations Implement Effective Safety Audits?
Implementing a successful safety audit program begins with planning and organization. Companies must first establish clear objectives for what they want to achieve with the audits. This might include reducing theft, preventing spoilage, or ensuring compliance with safety regulations. Once objectives are set, a comprehensive checklist is developed to cover all critical areas, from physical security measures to procedural guidelines and staff performance.
Training is another essential element. Employees should understand the importance of these audits and how their daily actions contribute to overall safety. Regular training sessions and clear communication help foster a culture where everyone is aware of their responsibilities in maintaining a secure environment. Additionally, assigning dedicated personnel to oversee the audit process can ensure that it remains a consistent part of the organization’s routine.
What Role Does Technology Play in Enhancing Safety Audits?
Modern technology offers several tools that can significantly improve the effectiveness of safety audits in logistics and distribution. Digital inventory management systems, for example, provide real-time data that can quickly highlight discrepancies or irregularities. When combined with automated reporting tools, these systems can alert managers to potential issues as they occur, rather than waiting for periodic manual reviews.
Surveillance systems integrated with analytics software are another asset. They not only record activities in storage areas and loading docks but also use data analysis to detect unusual patterns, such as unexpected gaps in staffing or unusual activity during off-hours. The use of mobile devices for on-the-spot reporting further enhances the speed and accuracy of audits, ensuring that valuable information is captured immediately.
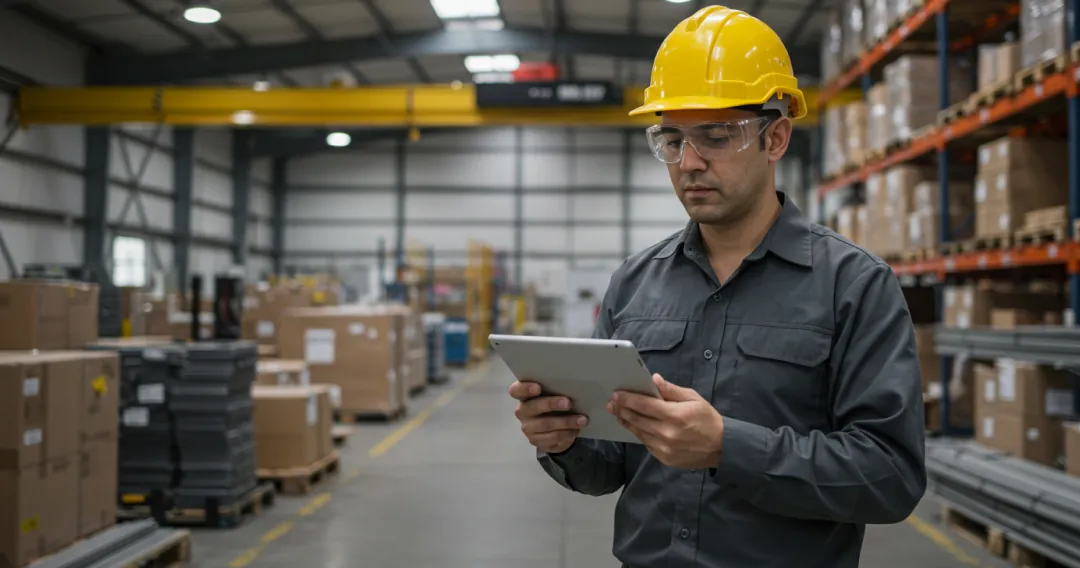
How ThinkLP Supports Logistics and Distribution Safety Audits
ThinkLP offers a platform that centralizes data from various sources, making it easier for organizations to conduct comprehensive safety audits. With ThinkLP, loss prevention teams can capture incident reports, audit results, and surveillance data all in one place. This integration not only saves time but also improves the quality of the data collected, making it easier to spot trends and address issues quickly.
The ThinkLP platform is designed to be user-friendly, enabling staff to input data directly from mobile devices and access real-time analytics. This capability ensures that even when incidents occur on the shop floor or during transit, the information is immediately available to decision-makers. By supporting a more connected and data-driven approach to audits, ThinkLP helps organizations improve their overall safety standards and reduce risks across the board.
What Challenges Should Organizations Expect?
Despite the clear benefits, implementing logistics and distribution safety audits is not without its challenges. One common issue is ensuring data accuracy. Inconsistent or incomplete data can lead to misguided conclusions, so maintaining high standards in data collection is essential. Another challenge is integrating new audit systems with existing operational processes. Organizations may need to invest time and resources in training staff and updating legacy systems to ensure a smooth transition.
Furthermore, as supply chains become more complex, the scope of audits must also expand. This means that auditors must be prepared to evaluate a wide range of factors—from digital security measures to physical asset management—which requires a broad base of knowledge and expertise. Overcoming these challenges requires commitment from all levels of the organization, along with the right technological support to streamline the process.
How to Stay Ahead in a Dynamic Environment
Looking to the future, the importance of regular safety audits in logistics and distribution will only increase. As businesses adopt more sophisticated technologies and face new regulatory requirements, the methods used for audits will evolve. Companies that invest in continuous improvement and keep abreast of industry best practices are better positioned to mitigate risks and ensure that their operations run smoothly.
Building a robust audit program is not a one-time effort. It involves ongoing assessment and adjustment as new risks emerge and operational environments change. By staying proactive and investing in both people and technology, organizations can maintain high standards of safety and efficiency in their logistics and distribution processes.
Explore ThinkLP’s Blog
Now that you know more about logistics and distribution safety audits, you can find additional insights on loss prevention and safety intelligence on ThinkLP’s blog. The blog features articles, case studies, and industry insights that provide practical tips and strategies for improving your loss prevention efforts.
Request a Demo
If you are interested in how ThinkLP’s software can support your loss prevention initiatives, we invite you to request a demo. Their Loss & Safety Intelligence Platform is designed to integrate with your existing operations, helping you reduce risks and improve efficiency. Reach out today to learn how ThinkLP can assist your organization in optimizing its loss prevention strategy.