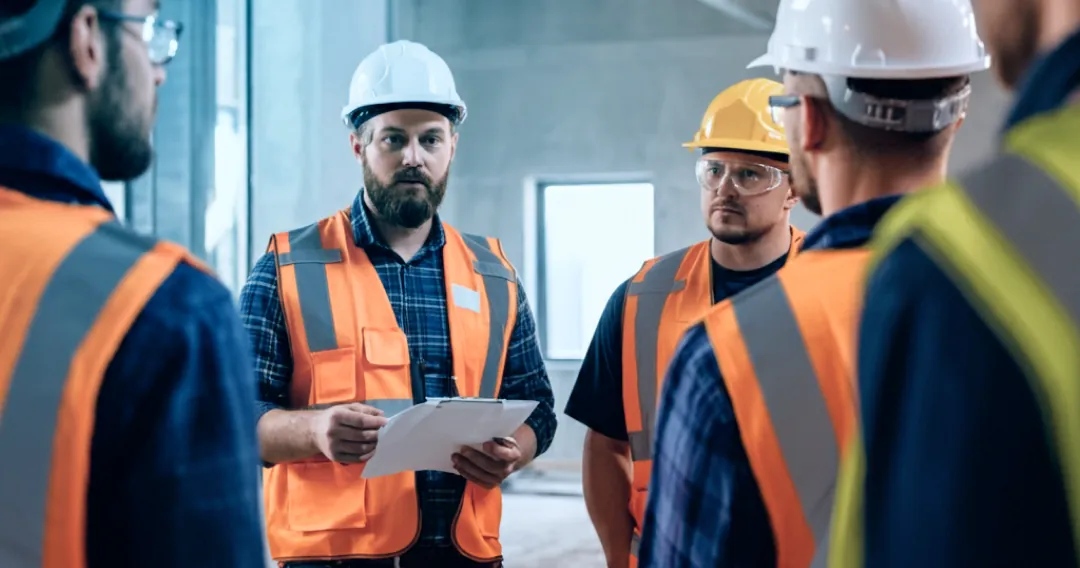
Complete Guide to OSHA Compliance: Requirements, Benefits, and Best Practices
In the second episode of It’s Your Loss, hosts Johnny Custer and Tony Sheppard sit down with retail industry titan and occasional antique treasure hunter, Rhett Asher. Yes, really. You came for the loss prevention talk and stayed for the Kim Possible theme song and a spontaneous antiquing confession.
This episode goes far beyond catch-and-detain stories. Rhett dives deep into his decades-long retail journey, from loading trucks to running operations for national retailers, to eventually becoming a cornerstone of LP’s evolution through leadership roles at RILA, NRF, FMI, the Loss Prevention Foundation, ThinkLP… and now, as SVP at ALTO Alliance.
Rhett’s not your average LP executive. His story starts in retail warehouses and takes wild turns through best-in-class stores, high-level ops roles, and an unexpected career leap into retail associations. Along the way, he mentored employees, rebuilt LP programs, coached youth soccer like it was the Premier League (seriously, he made teams quit mid-game), and helped elevate LP into a strategic discipline.
Now at ALTO, Rhett leads sales, marketing, and partnership development, building bridges between retailers, law enforcement, prosecutors, and community stakeholders to hold not just offenders accountable but the entire ecosystem that enables retail crime.
PODCAST EMBED
Highlights You Don’t Want to Miss
This episode is about more than one man’s impressive resume. It’s a crash course in how collaboration, curiosity, and humility can shape an entire industry. Rhett’s story is proof that the best LP leaders don’t just catch bad guys, they connect people, advocate for change, and maybe, just maybe, spot a killer deal in a vintage shop.
- The Alto Approach: Rhett explains how ALTO goes beyond traditional LP by connecting retail incident data with community response to actually solve the problem, recidivism and all.
- Total Retail Loss: From believing shrink was just “stuff people steal” to becoming a champion for margin, spoilage, and operational loss.
From Retail to the Vendor Side: Insights on how Rhett moved from operations to association leadership and shaped conversations that still impact LP strategy today. - Bringing legitimacy to LP: Rhett shares how he helped kick off the Loss Prevention Foundation and fought for LP’s legitimacy in the professional world. (Spoiler: It worked.)
- Antiques and Animated Crime Fighters: Somewhere between Kim Possible and a Joe LaRocca story, we find out Rhett’s favorite downtime activity, and it’s the last thing you’d expect from a guy who once ran ORC roundtables.
- The ThinkLP + ALTO Partnership: Johnny, Tony, and Rhett unpack how the two platforms are teaming up to combine deep analytics with on-the-ground action, bridging data and legal accountability in ways that could seriously move the industry forward.
Why Listen?
If you’re in LP, retail ops, risk management, or if you’ve ever been told to “stay in your lane.” this episode is for you. You’ll walk away with insights on industry innovation, leadership, real-world accountability, and why data is only valuable if you actually do something with it.
🎧 Listen now wherever you get your podcasts, and don’t forget to subscribe, share with your team, and maybe hum a little Kim Possible on the way out.
So buckle up, subscribe on your platform of choice:
And follow Tony and Johnny on Linkedin to join the conversation. Because when it comes to protecting profits—and your sanity—it’s your loss if you miss this.