The Real Cost of Inaccurate Counts
Inventory counting errors might seem like minor discrepancies, but their impact can be substantial. These errors can lead to significant financial consequences across various aspects of a business. Revenue losses occur when understocking results in missed sales opportunities. Increased costs arise from additional labor required for recounting and auditing, as well as potential expedited shipping to fill unexpected stock gaps. Profit margins can shrink due to markdowns on overstocked items.
Moreover, inventory discrepancies can distort financial statements, potentially leading to overestimated profits and incorrect tax filings. Operational inefficiencies, such as supply chain disruptions and warehouse inefficiency, further increase costs. In some cases, inventory errors can even result in compliance issues, leading to fines and legal complications.
Common Causes of Inventory Counting Errors
Several factors contribute to inventory counting errors. Human error is often the primary culprit. Manual counting processes are prone to mistakes, especially when dealing with large quantities or similar-looking items. Fatigue, distractions, and lack of proper training can all lead to inaccurate counts.
Another significant cause is poor inventory management systems. Outdated or inadequate software can make it difficult to track inventory accurately, especially across multiple locations or channels. Without real-time updates and synchronization, discrepancies can quickly accumulate.
Theft and shrinkage also play a role in inventory discrepancies. Whether it’s employee theft, shoplifting, or vendor fraud, these losses can create significant gaps between recorded and actual inventory levels.
The Ripple Effect on Business Operations
Inventory counting errors don’t just affect the immediate stock levels; they can have far-reaching consequences for a business. Inaccurate inventory data can lead to poor decision-making in purchasing, pricing, and sales strategies. For example, a company might order more stock of an item that appears to be selling well, only to discover later that the high sales numbers were due to counting errors rather than actual demand.
These errors can also impact financial reporting. Inventory is often a significant asset on a company’s balance sheet, and inaccuracies can lead to misstatements in financial reports. This can cause issues with investors, creditors, and regulatory bodies
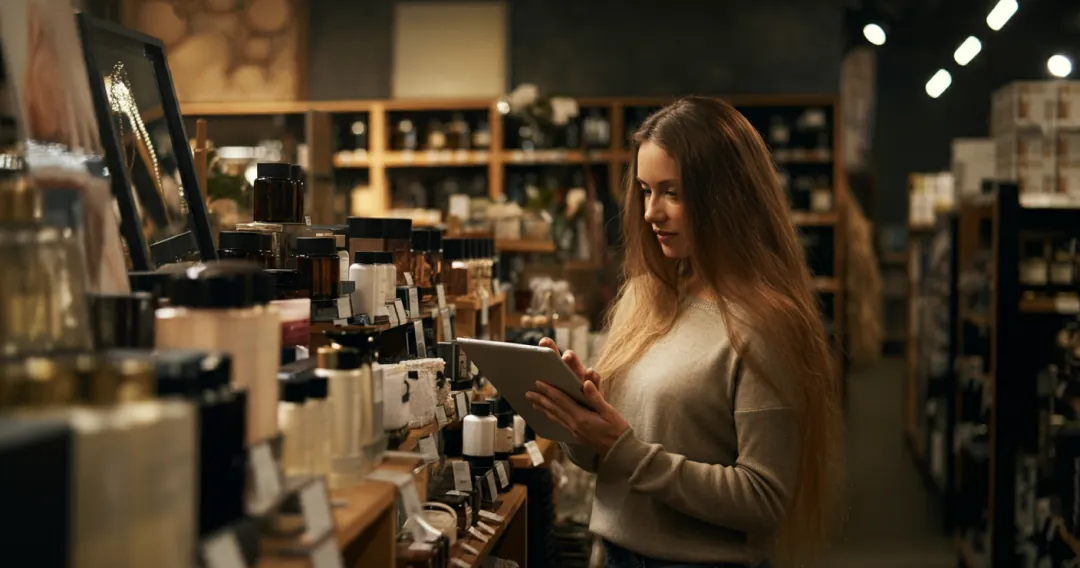
5 Best Strategies to Minimize Inventory Counting Errors
1. Implement a Robust Inventory Management System
Addressing inventory counting errors requires a multi-faceted approach. One of the most effective strategies is implementing a robust inventory management system. Modern software solutions can automate many aspects of inventory tracking, reducing the likelihood of human error.
2. Conduct Regular Cycle Counting
Regular cycle counting is another crucial practice. Instead of relying solely on annual physical counts, businesses should perform frequent counts of smaller sections of inventory. This approach helps identify discrepancies early and makes the counting process more manageable.
3. Provide Comprehensive Employee Training
Employee training is also essential. Staff members involved in inventory management should receive comprehensive training on proper counting techniques, the importance of accuracy, and how to use inventory management tools effectively.
4. Leverage Technology for Accurate Tracking
Technology plays a crucial role in minimizing inventory counting errors. Barcode systems and RFID tags can significantly improve accuracy and efficiency in tracking inventory movements. These technologies allow for quick and precise scanning of items, reducing the chances of manual counting errors.
5. Utilize Advanced Analytics Tools
Advanced analytics tools can also help identify patterns and anomalies in inventory data. By analyzing historical data and trends, businesses can predict potential issues and take proactive measures to prevent errors.
The Role of ThinkLP in Inventory Management
While not specifically designed for inventory management, ThinkLP’s platform offers valuable tools that can complement inventory control efforts. Their exception-based reporting and analytics capabilities can help identify unusual patterns in inventory data that might indicate counting errors or theft.
ThinkLP’s case management features can also be useful for investigating and documenting instances of significant inventory discrepancies. By centralizing this information, businesses can track trends over time and develop strategies to address recurring issues.
Creating a Culture of Accuracy
Beyond implementing systems and technologies, creating a culture that values accuracy is crucial for minimizing inventory counting errors. This involves setting clear expectations for inventory management, recognizing and rewarding accuracy, and fostering open communication about inventory-related issues.
Encouraging employees to report discrepancies promptly and without fear of repercussion can help catch errors early. Regular team meetings to discuss inventory challenges and brainstorm solutions can also contribute to a more accurate and efficient inventory management process.
Final Thoughts on Inventory Counting Errors
Inventory counting errors may be a common challenge, but they are not insurmountable. By implementing robust systems, leveraging technology, training employees effectively, and fostering a culture of accuracy, businesses can significantly reduce these errors and their impact.
While tools like ThinkLP can support aspects of inventory management through analytics and case management, a comprehensive approach that combines technology, processes, and people is key to achieving and maintaining inventory accuracy. As businesses continue to prioritize this area, they’ll be better positioned to optimize their operations, satisfy customers, and protect their bottom line.
Explore ThinkLP’s Blog
Now that you know more about inventory counting errors, you can find additional insights on loss prevention and safety intelligence on ThinkLP’s blog. The blog features articles, case studies, and industry insights that provide practical tips and strategies for improving your loss prevention efforts.
Request a Demo
If you are interested in how ThinkLP’s software can support your loss prevention initiatives, we invite you to request a demo. Their Loss & Safety Intelligence Platform is designed to integrate with your existing operations, helping you reduce risks and improve efficiency. Reach out today to learn how ThinkLP can assist your organization in optimizing its loss prevention strategy.